
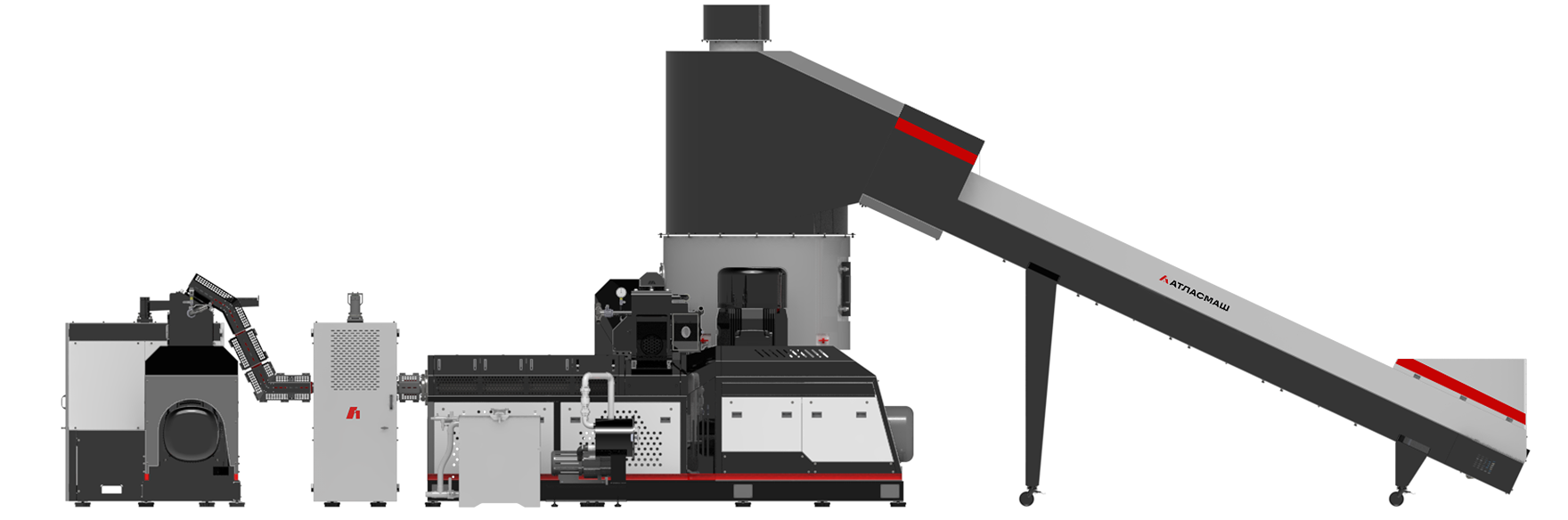
Industrial Single-Shaft Shredders for Plastics (WN Series)
The preferred choice for companies specializing in polymer recycling. Delivers a throughput of 250–1000 kg/h for plastic waste with minimal investment. Throughput is based on a 50mm installed screen mesh and may vary depending on screen size, material type, shape, density, and hopper load. Performance can be enhanced with optional upgrades available for each shredder model.
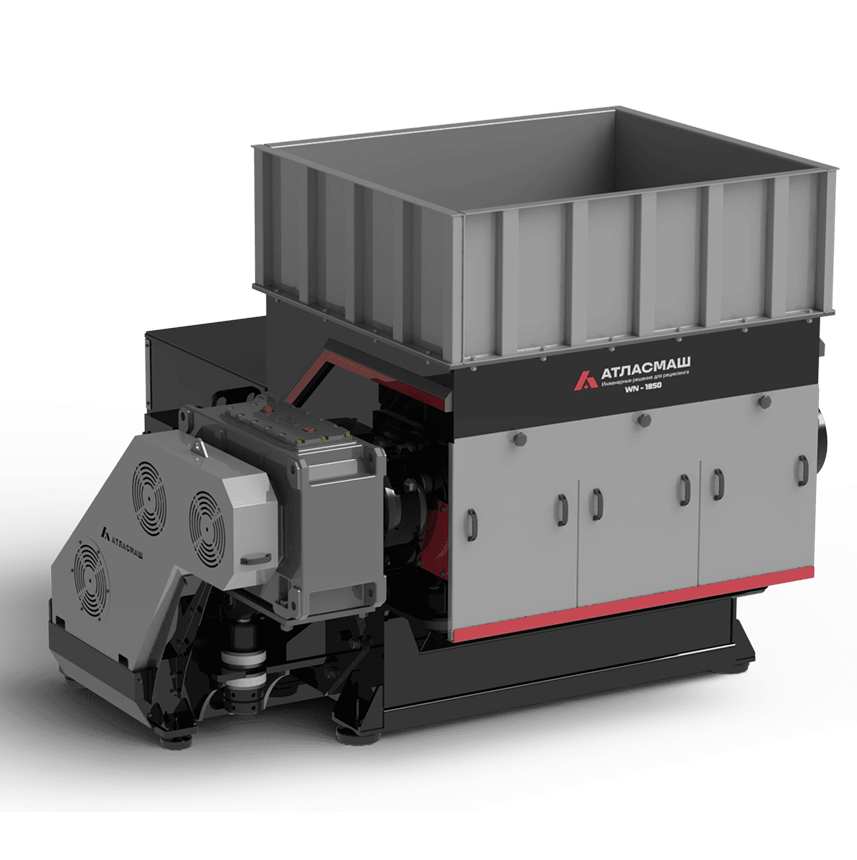
Advantages
High throughput.
Ergonomic design.
Easy installation, operation, and maintenance.
4-sided reinforced blades (thicker than imported alternatives).
Special shredding chamber design for large-diameter polymer waste.
Laser Filters F1
High-quality, uninterrupted polymer melt filtration for both industrial and contaminated plastic waste (PP, PE, PS, ABS, PVC, etc., including foamed materials).
Effectively removes contaminants like ferrous/non-ferrous metals, wood, paper, textiles, fibers, unmelted plastics, sand, stones, etc., with minimal material loss—all without operator intervention.
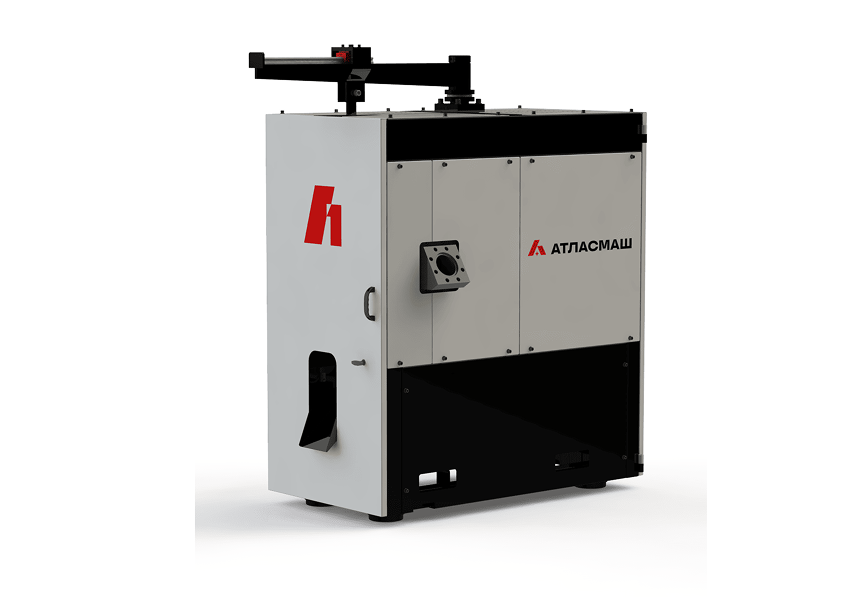
Advantages
Long-lasting filter screens.
Large filtration area (4000 cm²).
Handles both standard (200–600 µm) and fine (down to 120 µm) filtration.
User-friendly operation.
Turnkey integration with extruders from any manufacturer.
RX Series Plastic Pelletizing Lines
Versatile pelletizing lines capable of processing heavily printed films and HDPE pipes at high throughput. The RX series handles challenging plastics—fibers, rigid polymers, 100% printed films, and high-moisture materials—that are unprocessable by other granulators.
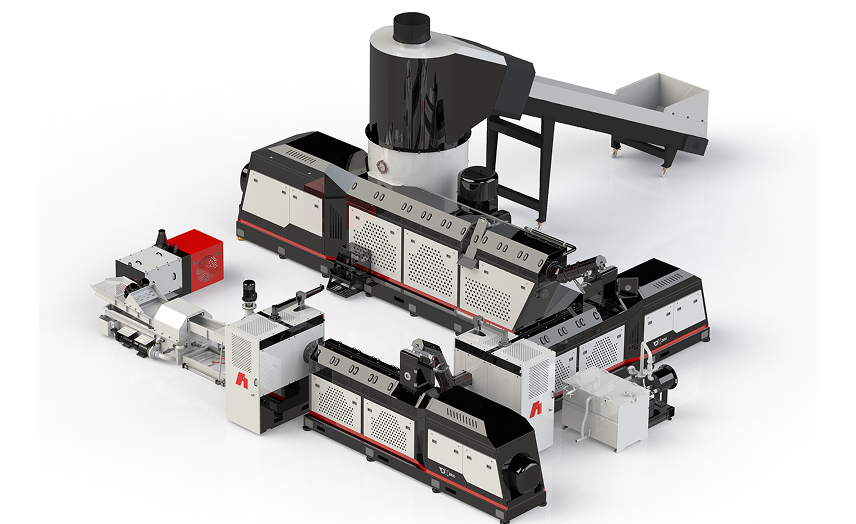
Advantages
Produces high-quality recycled pellets from film and rigid waste.
Real-time monitoring.
Configurable with 1, 2, or 3 cascades.
Dual large-area laser filters.
Throughput up to 2 tons/hour.
Three extruders in one line.
Two vacuum degassing zones between extruders.
Centrifuge C750
Inclined centrifuges are designed for spinning and washing various types of crushed polymers.
The raw material is fed into the centrifuge's loading chamber and moves toward the discharge zone by means of a rotating rotor. At this moment, the separation of material from water occurs, with the water passing through the mesh and draining to the outlet.
The cleaned and spun material from the centrifuge falls into a tank, press, or is transported further along the production line.
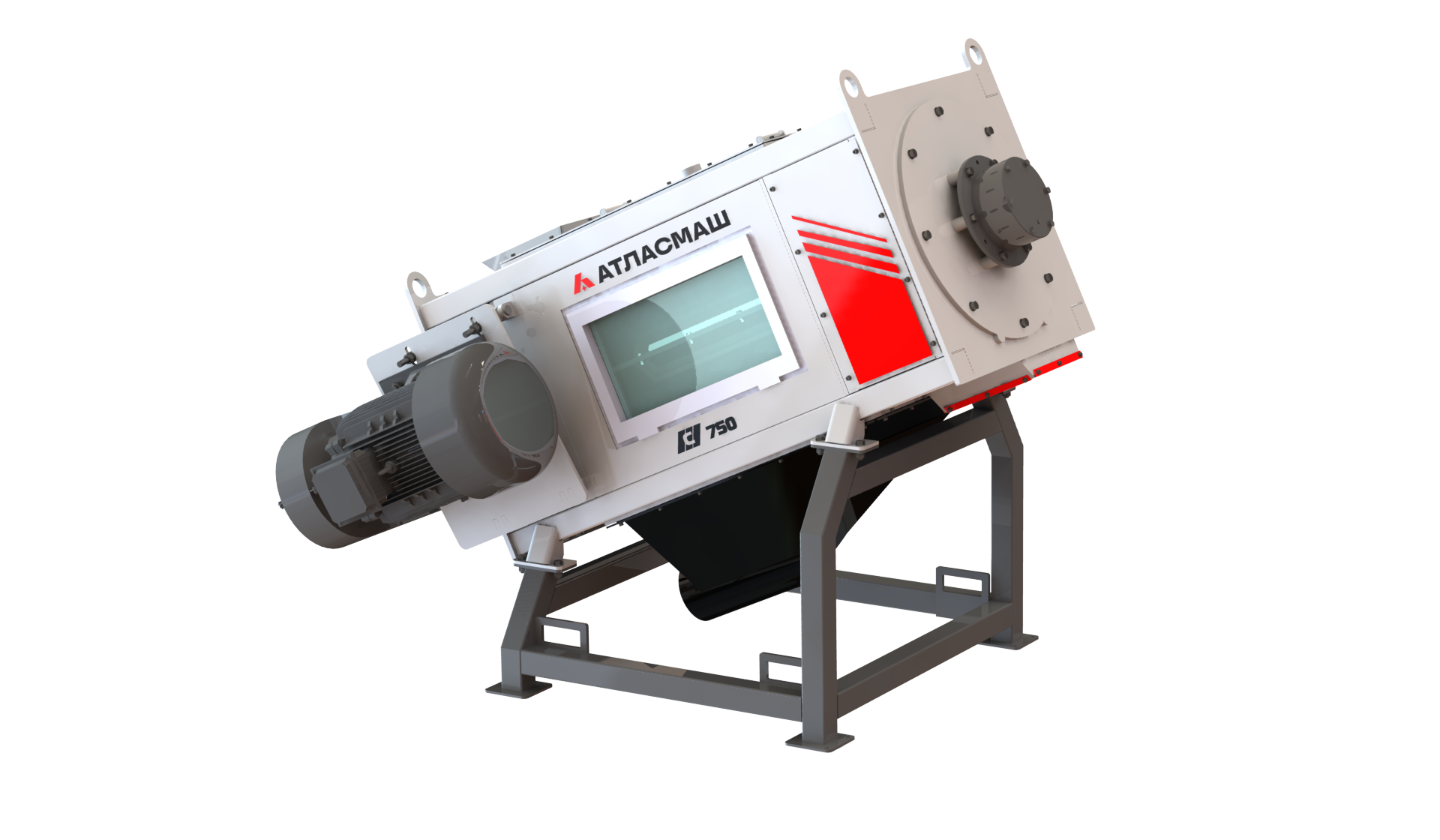
Advantages
Capacity from 500 to 2000 kg/hour
Replaceable blades made of wear-resistant steel
Construction - stainless steel and painted steel
Installation after flotation tank for first intensive friction washing of material
Storage Hopper
Typically used after washing lines and solves several tasks simultaneously:
Storage of washed crushed material in volumes from 6 to 15 cubic meters
Material homogenization (when processing waste, the material often comes non-uniform which negatively affects both the final product and the stability of the granulation process). Using an intermediate storage hopper that also mixes (homogenizes) the material solves this problem.
Dosing material feed to the next processing stage (into big bags, agglomerator or granulator).
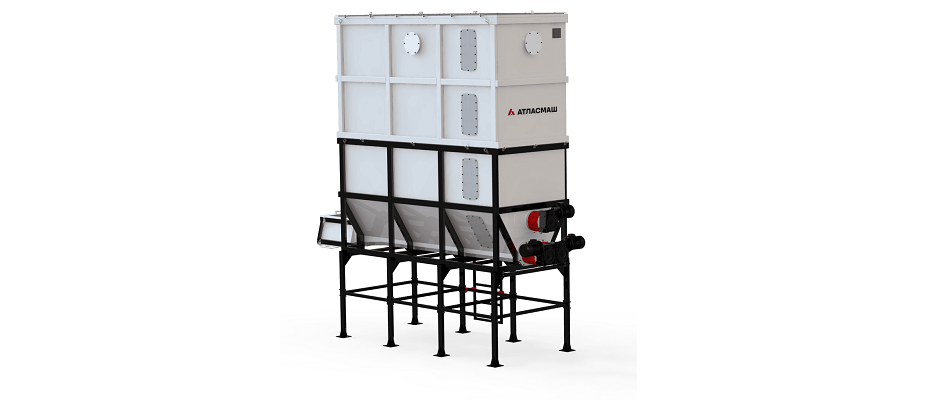
Learn all about reliable and high-performance recycling equipment
Fill out the form and we will contact you.